
Mehr als 15 Jahre erfolgreich unterwegs in der Ermittlung des Druckfilterwertes bei der Herstellung von Masterbatches und Compounds.

Alles fing 1998 an – damals gründeten mehrere Unternehmen das „CEN Committee Filtertest“ bestehend aus Masterbatch-Produzenten und Herstellern von Laboranlagen für die Kunststoffverarbeitung. Ziel dieser Initiative war es, eine standardisierte Methode zur Ermittlung des Druckfilterwertes zu entwickeln.
2004 war es dann schließlich soweit und das CEN Committee präsentierte mit der EN 13900-5 ein einheitliches Messverfahren, mit dem sich die Eignung von Pigmenten für die Färbung von Kunststoffen beschreiben lässt und das inzwischen als ISO 23900-5 auch schon internationaler Standard geworden ist.
Anwendung
Der Druckfiltertest dient dazu Qualitätsunterschiede in einem Polymer aufgrund von Agglomeraten, unzureichend dispergierten Füllstoffen bzw. Verunreinigungen zu erkennen.
Er kann eingesetzt werden z. B.
- im Bereich der Produktentwicklung zur Optimierung von Farbansätzen etc.
- zur Qualitätsüberwachung bzw. Aus- und Eingangskontrolle von Masterbatchen, Compounds oder Polymeren
Funktion
Das zu prüfende Material wird in einem Extruder aufgeschmolzen, homogenisiert und über eine Schmelzepumpe mit einem definierten und konstanten Volumenstrom durch ein Sieb gefördert. Partikel ab einer bestimmten Größe setzen das Sieb zu und verringern damit die freie Durchtrittsfläche des Siebs. Dadurch baut sich bei einem konstanten Volumenstrom vor dem Sieb ein größerer Druck auf, der von einem Sensor erfasst wird, und für eine Bestimmung der Probenqualität herangezogen werden kann.
Besondere Merkmale
- Ein Filterkassettensystem erlaubt einen Filterwechsel innerhalb weniger Sekunden.
- Zum Wechseln des Filters kann über ein Bypassventil der Schmelzefluss vor dem Filter umgeleitet werden. Das erlaubt eine Unterbrechung des Schmelzeflusses durch den Filter, ohne den Extruder und die Schmelzepumpe stoppen und nach dem Filterwechsel wieder anfahren zu müssen.
- Integrierte Vorheizung des Siebes
- Einfach zu bedienende Software zur Berechnung des Druckfilterwertes und Erstellung eines Protokollausdrucks
Wie funktioniert der Filterwechsel in weniger als 10 Sekunden?
- Einlegen der Kassette mit Filter (S1) in die Führungsschiene
- Durch Schwenken der Schmelzeweiche (W) Umlenken des Schmelzeflusses in den Bypass (B).
- Lösen der Filterkassettenfixierung (P). (nicht dargestellt)
- Einschieben der eingelegten Filterkassette (S1) in die Vorheizposition (S2) und Weiterschieben der Filterkassette aus der Vorheizposition (S2) in die Prüfposition (S3). Gleichzeitig wird der benutzte Filter (S3) verschoben in die Entnahmeposition (S4).
- Fixieren der Filterkassette (S3).
- Durch Rückschwenken der Schmelzeweiche Rückleitung des Schmelzeflusses durch den Filter.
- Entnehmen der Filterkassette (S4).
Ex Extruder mit Schnecke (schematisch dargestellt)
Mp Schmelzepumpe (schematisch dargestellt)
P1 Massedruck im Extruder
P2 Massedruck vor dem Filter
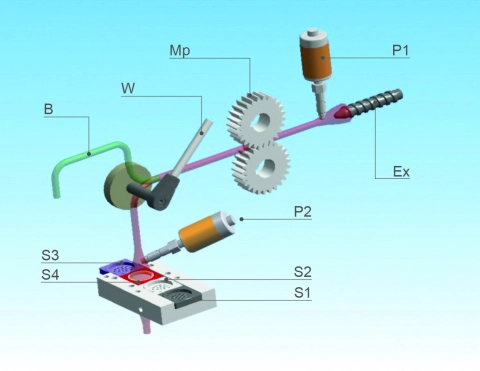
Messwerterfassung
Eine Druckfiltertest-Unit mit einem integrierten Touch Panel CMI 7 erfasst die Testdaten:
- Schmelzedruck vor dem Filter
- Schmelzetemperatur
- Schmelzepumpendrehzahl
Die zeitlichen Verläufe von Schmelzedruck und -temperatur werden in einem Diagramm dargestellt.
Über einen Start- und Stop-Button gibt der Benutzer den Beginn (Einfüllen der Probe) und das Ende des Tests vor. Die Berechnung des Druckfilterwertes (FPV = Filter Pressure Value) erfolgt am Ende des Tests durch Ermittlung des Anfangsdrucks PStart bzw. des während des Tests aufgetretenen maximalen Drucks Pmax und Verwendung der Formel:
FPV = (Pmax– PStart) / m
*m ist das in der Probe enthaltene Pigmentgewicht.
Die aufgezeichneten Daten können im Collin Microcontroller abgespeichert und ein Testprotokoll kann ausgedruckt werden.
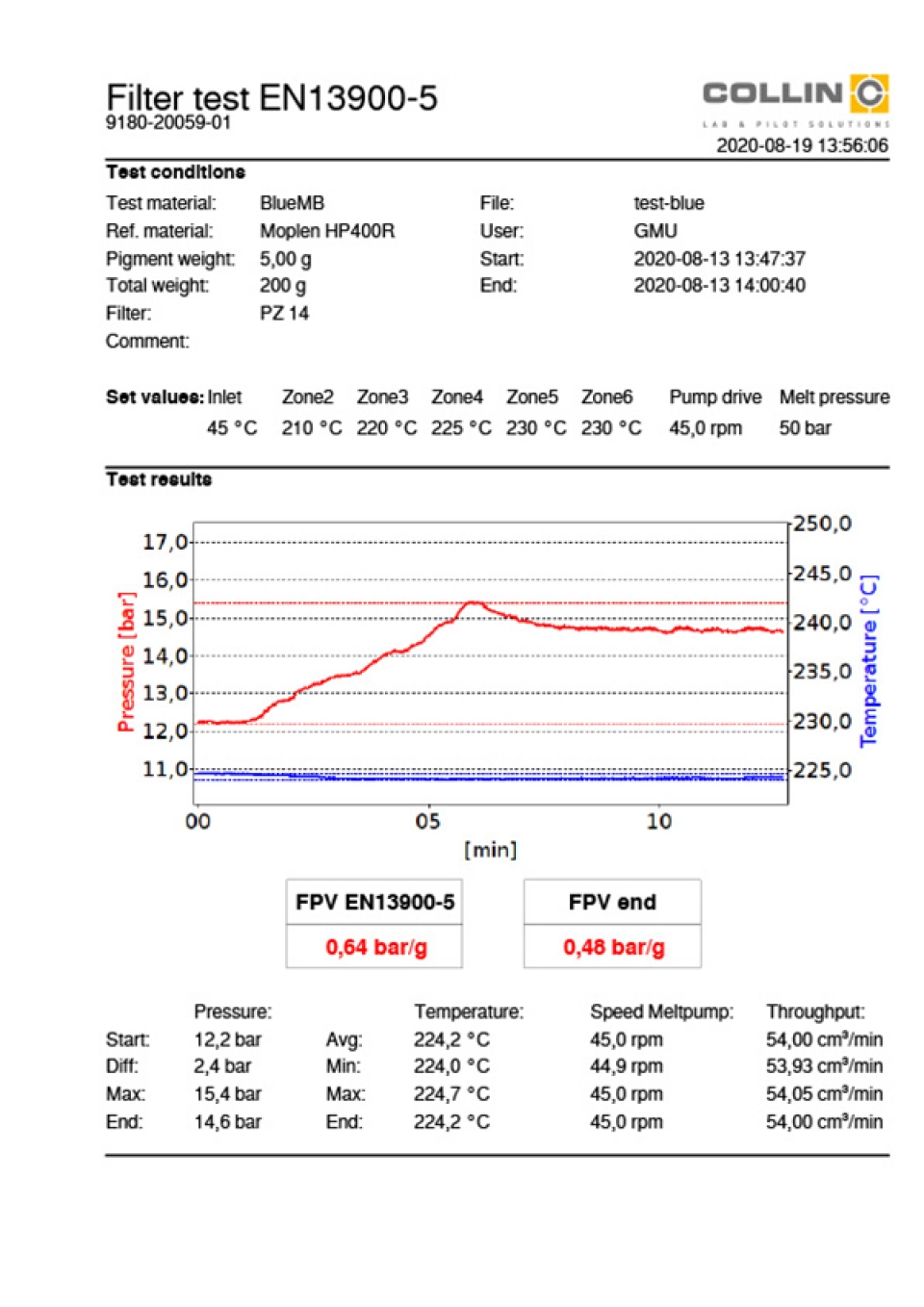